What Is Carbonwood?
In this article, Martin Hopley asks what is carbonwood and speaks to the experts at TaylorMade to find out
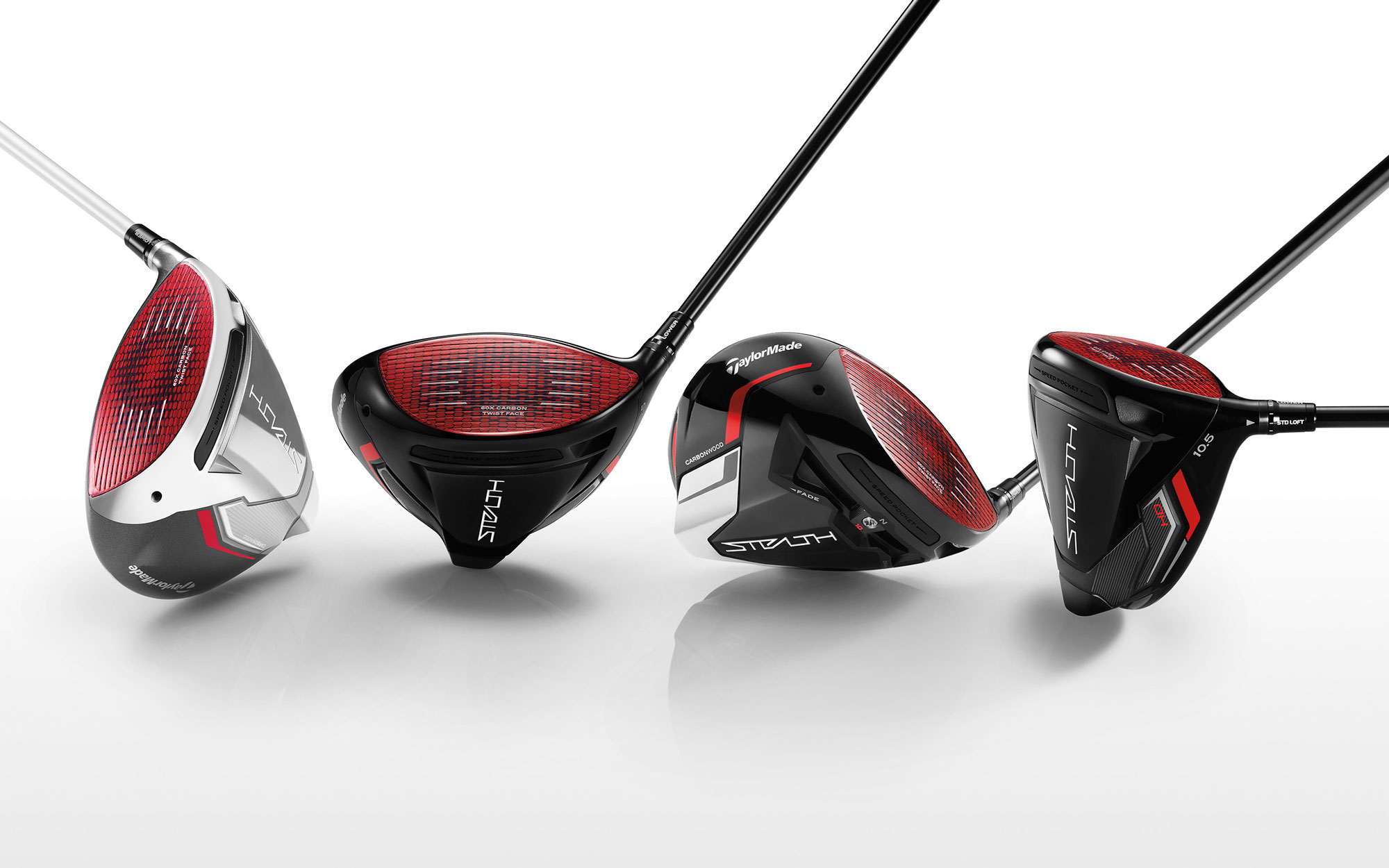
What Is Carbonwood?
The TaylorMade Stealth driver was launched with much fanfare at the start of the year as the brand heralded the beginning of the Carbonwood age. So, what is meant by this? TaylorMade is renowned for bringing the buzz to its marketing, but this time it’s different as we take you behind the scenes to give you the background to this claim.
To understand the idea of the Carbonwood age, we have to go back in time to when TaylorMade was the pioneer of the metalwoods era with heads made from steel. When the limits of steel were reached, a lighter, stronger material in titanium took over to extend the metalwood era. The goal was always to find materials that were lighter and stronger, and by 2000 TaylorMade decided to look to the next material that would deliver this, namely carbon composite.
Carbon faces are better than titanium because they are lighter and stronger, which means that weight saved from the face can be redistributed elsewhere to improve the performance and forgiveness of the head. Carbon also flexes differently to metal and is therefore more efficient at retaining energy within the ball at impact, increasing ball speed and distance.
Some other brands launched carbon-faced drivers around the turn of the century, but the performance benefits of the technology were easily caught up by advances in titanium drivers as not enough was known about how carbon could be produced effectively. TaylorMade looked, learned and realised it needed to find the right level of face flexibility and durability to withstand the high- speed impacts of a driver with a golf ball. It was the start of a two-decade journey.
Joining TaylorMade around this time was composite specialist Mark Greaney, who, as Head of Advanced Technology, took over the carbon-face project in 2003. His first job was to ensure the material could be made in a way that meant it could be used in a driver face. Up until this point, carbon has been created in large pieces for use in things like planes and cars, where there are less repetitive impacts and therefore any tiny air pockets or voids in the materials would not matter as much.
In a driver face, repeating strikes on these voids at high speed would cause the material to break down, so new manufacturing processes had to be created to make the carbon void-free. The method of inspection for voids this small did not exist in the composite industry, therefore TaylorMade’s R&D team had to turn to ultrasonic scanners from the microchip sector to control for sub-millimetre air pockets.
Carbon is made up of fibres and is very strong in one direction, but not every direction. To make a face that was fast and durable, Greaney and his team focused on finding the right carbon fiber and resin combination. In addition, the orientation of the fibers is crucial for maximum performance. There are 60 layers of carbon in the Stealth driver face, and to get to this point, TaylorMade spent years solving the conundrum of how to combine the right thickness of the layers with the right number of layers, and then how to optimise orientation. In fact, the research and development to create a fast and durable face took almost a decade.
Now it had the strength, it had to overcome one downside to composites – they are susceptible to abrasion. TaylorMade spent a year testing over 50 different formulations to come up with a polymer that could withstand the toughest of environments. However, when it was tested, it was discovered that in wet conditions the ball could skid up the face, producing shorter shots. By adding scorelines, it was able to overcome this issue.
Lastly, TaylorMade discovered there was a spin and launch penalty as compared with a titanium driver. It took another year of research, evaluating over 100 texture patterns, before Greaney and his team ultimately landed on the nanotexture cover. This cover allows the face to not only have the highest ball speed, but also the optimum launch conditions – all while being able to withstand thousands of shots.
To test its carbon face in the market, TaylorMade launched the Glorie Reserve driver in Japan in 2012. It was a manufacturing success, but not a commercial one due to the $1000 price tag – visually it was a bit challenged and the aerodynamics had yet to be figured out for the new material. However, it did prove the carbon face was robust enough to work in a commercial product.
Carbon parts at this point in time were made in large sizes and small quantities for things like Formula 1 cars. So, there was no one around who could make small driver faces in large quantities to the exacting standards required, and at a price that golfers would pay – especially when TaylorMade knew it could still match the performance benefits with titanium faces for now. Therefore, the project was shelved in 2015, but the time invested was already creating benefits as learnings from the head design of the research fed their way into the SLDR driver and the carbon crown of the M1 and M2 drivers.
However, a year later, the CT rules governing faces were changed to cover the whole of the face and not just the middle. This meant weight would need to be added to the titanium face to make it compliant, which would limit the future potential gains of the material. As such, it was clear to TaylorMade the days of metal faces were numbered.
Therefore, from 2017, TaylorMade R&D went all in on carbon faces to design a head structure that would work with the face, use the saved weight to make the head more rigid and also place the weight further back to improve launch and ball speed.
Heading into 2019, it was all ready to go, but no one could make carbon faces in this quantity to the brand’s specification. So TaylorMade decided to create its own production plant in Taiwan and design its own machines to deliver the carbon face in large quantities at a price that would be economical for the company to sell at. Then the pandemic hit.
It’s one thing building a new production plant using a different material on new machines to create a unique product in another country. To then have to do it remotely over video calls instead of seeing the process first-hand brought another level of complexity, but TaylorMade pulled it off.
Twenty-one years after TaylorMade embarked on the journey, the Carbonwood era has come of age. Head of Product Innovation Tomo Bystedt says there is no turning back.
“We are in a great place with a new platform and there is a lot of learning, development, improvement and refinement that can happen. Obviously we have things in the pipeline for the next couple of years, but beyond that, who knows. Ultimately, the biggest benefit is making clubs better for the average golfer so they are easy to hit, more forgiving, more consistent and straighter,” he says.
Subscribe to the Golf Monthly newsletter to stay up to date with all the latest tour news, equipment news, reviews, head-to-heads and buyer’s guides from our team of experienced experts.
Martin Hopley is one of the foremost UK equipment reviewers with over 20 years' experience. As the former founder of Golfalot.com he was an early pioneer of online reviews and has also been a regular contributor to other titles. He is renowned for his technical knowledge and in-depth analysis, which he now brings to Golf Monthly.
-
Ryder Cup 2025: Which Players Are In Contention For Keegan Bradley's Six Wildcard Picks?
With Keegan Bradley close to revealing his captain’s picks for the US Ryder Cup team, here are some of the main contenders for one of the final six places
-
Keegan Bradley Hints At US Ryder Cup Wildcard Surprises
The US Ryder Cup captain has hinted that some players who think they’ll be given a wildcard for the match may be left disappointed